Holcim se distingue par ses solutions intégrées, son expertise et ses produits spéciaux
Le 21 Juillet 2020
De la mi-2019 à la fin 2020, les CFF rénovent la ligne ferroviaire entre Zoug et Arth-Goldau sur un tronçon de 15 kilomètres. Outre le tracé, l’assainissement concerne aussi les tunnels, les ponts, la technique ferroviaire et les voies. Holcim a soutenu ce gros projet en fournissant des solutions intégrées, des produits spéciaux, son expertise et en mettant l’accent sur l’efficacité, la rentabilité et la préservation des ressources.
Construite il y a plus d’une centaine d’années, la ligne de chemin de fer sur la rive est du lac de Zoug est située dans une zone sensible en termes de topographie et d’aménagement du territoire. Le principal défi du projet était l’espace très restreint par endroits qui exigeait une planification d’autant plus précise des différentes étapes de travail et de la logistique. C’est notamment lors de l’évacuation des gravats et de la livraison des matériaux de construction qu’Holcim a pu se distinguer avec ses services et sa logistique sur-mesure.
Valorisation des matériaux issus de la démolition et fermeture du cycle des matériaux
Holcim a organisé l’évacuation de 170’000 tonnes d’excavation et de gravats des tunnels, des voies et des murs. Le transport de telles quantités a nécessité 6’800 trajets en camion. Avant d’être évacués, les matériaux ont été analysés et triés sur place par des experts en pédologie et en sciences de l’environnement. Holcim a traité près de 6’000 tonnes de matériaux rocheux et de déblais propres sur son site de Brunnen et les a réutilisé pour le remblai. La réutilisation des matériaux issus de la démolition préserve les matières premières primaires et évite d’encombrer les décharges. Les matériaux non réutilisables ont été soit mis en dépôt dans notre gravière de Brunnen, soit éliminés dans les règles de l’art dans une décharge, l’accent ayant été mis sur la réduction des distances de transport lors de la planification.
14 granulats différents
Le site de Brunnen a non seulement traité les gravats, mais aussi livré 14 sortes de roches différentes: notamment du concassé pour gabions, des granulats non gélifs, du remblai pour la construction des voies, des matériaux filtrants et du ballast concassé.
Un laboratoire sur place pour contrôler le béton spécial
Holcim a également fourni du béton maigre, du béton de construction et du béton projeté. Les travaux sur les tunnels ont impliqué l’utilisation d’un béton spécial autoplaçant et résistant au gel. Afin de réduire au maximum la pression du coffrage, le temps de fin de prise a été fixé à 7 heures. Avant la mise en place, un essai de slump flow et un contrôle de la teneur en air ont été réalisés sur chaque chargement de camion. Holcim avait installé pour ce faire un laboratoire sur place. Au total, 26’000 m3 de béton ont été nécessaires. Près d’un quart était constitué de béton maigre recyclé et environ la moitié du béton de construction contenait le ciment Susteno qui préserve les ressources naturelles.
Un interlocuteur unique
Pour le consortium ARGE ZUGO en charge de l’exécution du chantier, la décision de confier la mission à Holcim a été motivée en premier lieu par le concept global et les différents services proposés par l’entreprise, mais aussi par le savoir-faire technique et le soutien de Holcim pour les questions techniques. « Notre forte implantation locale nous a permis de nous procurer tous les produits (y compris les produits spéciaux) dans la région, que ce soit auprès de notre usine à Brunnen, à Küsnacht ou bien à Cham », explique René Küng, chef de projet et Technical Sales & Supply Chain Manager. « Ainsi, nous avons pu faire passer la majorité des trajets d’évacuation vers le sud par Arth-Goldau et contourner l’agglomération de Zoug. »
Contact médias
Notre service médias se tient à la disposition des journalistes pour répondre à leurs questions.
Téléphone: 058 850 68 48
E-Mail: communications-ch@holcim.com
Entretien avec René Küng, chef de projet et Technical Sales & Supply Chain Manager chez Holcim
« L’objectif est toujours de trouver la meilleure solution »
Quel était le plus grand défi de ce projet ?
Ce projet était extrêmement complexe du point de vue de la planification et de la logistique. Le tronçon en travaux s’étendait sur 15 kilomètres entre lac et montagne. Il n’y avait donc que deux voies d’accès pour assurer l’évacuation et la livraison quotidiennes de tous les matériaux. Les jours de pointe, 30 camions ont circulé, réalisant au total 200 rotations. La coordination des flux de matériaux a donc été le principal défi à relever.
Quelles sont les forces de Holcim dont vous avez pu tirer parti pour ce projet ?
Nous avons pu proposer un concept global. En tant que chef de projet sur le terrain, j’étais le premier interlocuteur du client concernant la logistique. J’ai planifié les livraisons quotidiennes à destination et en provenance des usines avec la gestionnaire logistique et ai tout coordonné, un service qui a épargné au client un travail long et fastidieux. Par ailleurs, nous avons pu trouver tous les matériaux, y compris les produits spéciaux, dans la région. Les courtes distances de transport entre nos usines et le chantier se sont avérées pertinentes tant sur le plan économique qu’écologique.
Qu’est-ce qui te motive dans des projets si complexes ?
Mon travail change tous les jours, tu ne sais jamais ce qui t’attend. L’objectif est toujours de trouver des solutions et d’en tirer le meilleur parti pour tous les acteurs impliqués. « Non » n’est pas une réponse. Tout problème a sa solution. Et je peux la proposer grâce à mon expérience et aux bonnes relations que j’ai établies avec les clients. Ils y sont extrêmement sensibles.
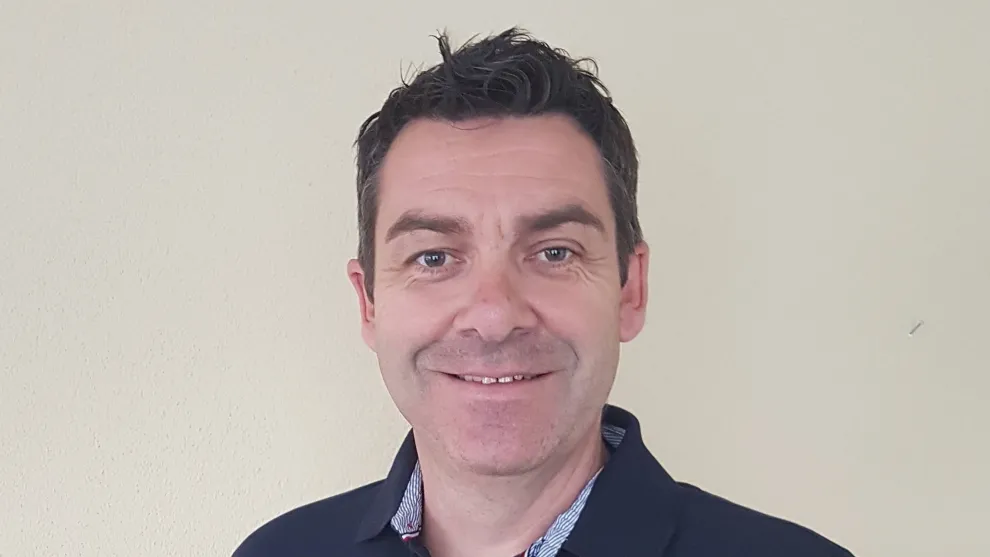