Ciments
Holcim (Suisse) SA offre une large palette de ciments et de liants hydrauliques, produits qui entrent dans les différentes applications techniques de la construction. Mis à part notre vaste assortiment en ciments standards et spéciaux, nous développons également des ciments sur mesure pour les besoins particuliers du client tant du point de vue technique qu'économique. Grâce à notre infrastructure de production flexible et à notre logistique de distribution fiable, nous pouvons en tout temps également livrer les ciments sur mesure en petite quantité.
Qu’est-ce que le ciment?
Le ciment est une poudre grise produite à partir de calcaire brûlé et d’argile, qui dispose de propriétés hydrauliques.
Dès qu’il est mélangé avec de l’eau, une réaction chimique se produit et le mélange durcit. Le ciment sert ainsi de liant qui, avec le sable, le gravier et les additifs, est transformé en béton, le matériau de construction le plus important de notre époque. Le ciment est aujourd’hui produit dans le monde entier selon le même procédé.
Comment se fabrique le ciment
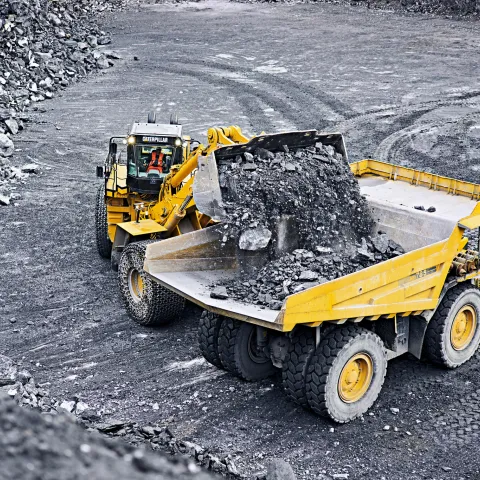
Carrière
Les mineurs extraient du calcaire (carbonate de calcium) et de la marne des carrières par explosion. Pour cela, ils forent dans le rocher des trous profonds qu'ils remplissent d'explosif. Les charges sont ensuite allumées d'après un échelonnement précis. La technique moderne de minage permet de réduire les vibrations et de faire tomber chaque tranche de paroi rocheuse de manière ordonnée.
Transport jusqu'au concasseur
Des chargeuses sur pneus et des dumpers permettent de transporter jusqu'au concasseur la pierre brute qui a été détachée du rocher par le tir de mine et qui atteint parfois une dimension d'un mètre. De puissants concasseurs à mâchoires ou à marteaux la réduisent à la taille d'un poing, voire d'une noix. Souvent, la matière est humide - notamment l'argile et la marne - et nécessite un séchage avant de pouvoir être concassée.
Transport jusque dans la cimenterie
Les matières concassées passent ensuite jusque dans la cimenterie. Cela se fait le plus souvent par bandes transporteuses, mais parfois par wagons, camions ou par un autre moyen de transport approprié.
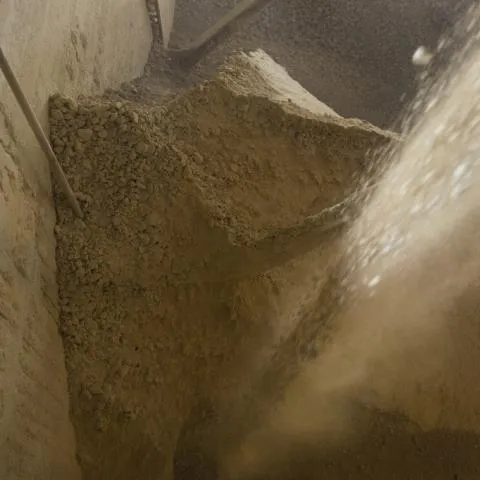
Lit de préhomogénéisation
La matière première pour la fabrication du ciment doit être constituée d'un mélange correctement dosé de carbonate de calcium, ainsi que d'oxydes de silicium, d'aluminium et de fer. Les matières extraites des carrières, puis concassées - soit le calcaire et la marne ou l'argile - doivent donc être soigneusement mélangées (préhomogénéisées); pour cela, elles sont mises en dépôt, dans la bonne proportion, par couches successives, ce qui donne un lit de préhomogénéisation; elles sont ensuite reprises par tranches obliques. La matière ainsi préparée peut être transférée dans le broyeur pour être réduite en farine.
Broyeur à farine
Un broyeur à galets réduit la matière première préhomogénéisée à l'é tat de farine. Ce résultat est obtenu par de gros galets qui écrasent les morceaux sur une assiette rotative jusqu'à ce que cette matière atteigne la finesse souhaitée. Lorsque ce point est atteint, le flux de gaz chauds sortant du four, qui sèche la matière dans le broyeur, emmène la farine. Celle-ci passe par un séparateur - sorte de filtre -, qui assure l'extraction, à destination du silo à farine, de la matière suffisamment broyée. Les opérations consistant à broyer, à séparer et à pulser la farine dans le silo ad hoc contribuent à l'homogénéisation de celle-ci.
Installation de filtration des gaz du four
L'énergie thermique produite par la flamme est utilisée de la manière la plus efficace possible : les gaz sortant du four servent à sécher la matière dans le broyeur à farine. Ils assurent aussi le transport de la farine crue à destination du silo à farine. L'i nstallation de filtration comporte des tissus très fins ou du feutre, qui retiennent des poussières particulièrement fines avant que les gaz soient rejetés dans l'atmosphère.
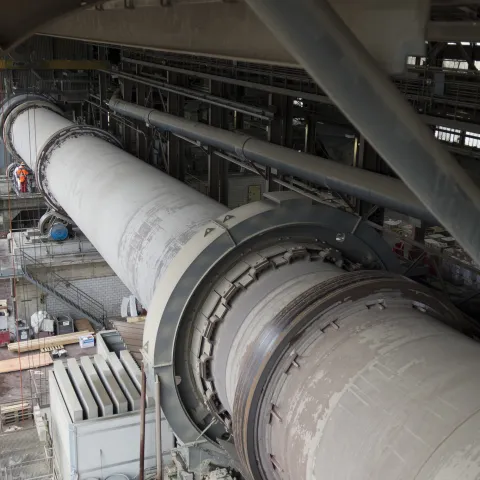
Préchauffage
L'échangeur à cyclones assure de manière optimale le préchauffage de la farine crue avant que celle-ci passe dans le four. Elle y rencontre les gaz chauds sortant du four et se trouve ainsi décarbonatée à hauteur de 20 à 40%, c'est-à-dire transformée en chaux calcinée. Cette opération consiste à extraire du calcaire le dioxyde de carbone qui y est lié.
Zyklon-Vorwärmer eignen sich optimal dafür, das Rohmehl aufzuheizen, bevor es in den Drehofen gelangt. Dabei erhitzen die
Ofenabgase das Rohmehl (Ofenmehl) im Gegenstrom in sehr effizienter Weise so weit, dass es bei Eintritt in den Ofen bereits zu 20 bis 40 % kalziniert, das heisst, in gebrannten Kalk umgewandelt ist. Gebrannter Kalk entsteht durch Austreiben des gebundenen Kohlenstoffdioxids aus dem Kalkstein.
Four rotatif
Le four est ainsi conçu qu'il assure le transfert de chaleur le plus efficace possible du combustible en flamme à la farine préchauffée. Avant d'entrer dans le four, celle-ci a déjà atteint la température de 1000° C. À l'intérieur, elle passe à 1450° C. À cette température élevée, les minéraux constituant la farine réagissent pour former du clinker, composé principalement de cristaux de silicate de calcium.
Refroidisseur à clinker
Le clinker doit ensuite être rapidement refroidi. Pour cela, on pulse de l'air tiré de l'atmosphère à travers la grille du refroidisseur, sur laquelle passe le clinker. Ce même air, ainsi préchauffé, alimentera le four en oxygène. Une telle récupération de chaleur assure l'utilisation optimale de l'énergie consommée. Le clinker quitte, à quelque 100° C, le refroidisseur sur un transporteur à plaques.
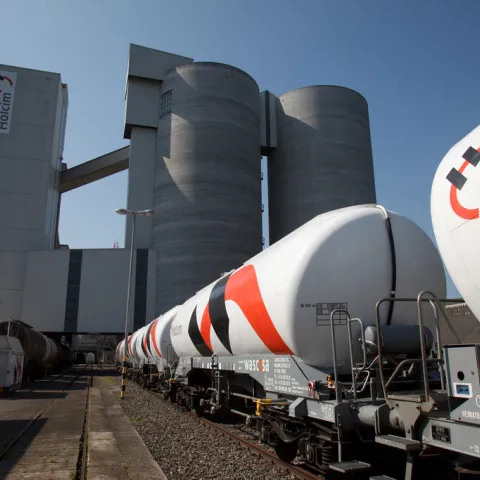
Silo à clinker
Des transporteurs à plaques amènent le clinker refroidi dans de grands silos ou dans une halle; là, il est stocké jusqu'à ce qu'on le broie pour en faire du ciment.
Broyeur à ciment
Dans ce broyeur, des boulets réduisent le clinker en une farine qui, moyennant adjonction d'environ 5% de gypse naturel ou synthétique, devient ainsi du ciment. On peut encore co-broyer d'autres ajouts à propriétés hydrauliques, tels que du laitier de haut fourneau, des cendres volantes ou de la pouzzolane; cela permet de conférer au ciment certaines propriétés spécifiques.
Logistique
Le processus de fabrication terminé, le ciment est ensaché à destination du commerce ou livré aux utilisateurs en vrac, dans des véhicules spéciaux. Le mode de transport dépend à la fois de l'emplacement de la cimenterie et de celui du destinataire; suivant les cas, on recourra au rail, à la route ou à la voie d'eau.